Principles of Aluminum Extrusion
Aluminum extrusion is a plastic processing method that applies external force to a metal billet placed in a container (extrusion barrel), causing it to flow out from specific die holes to obtain the desired cross-sectional shape and dimensions.
Composition of Aluminum Extrusion Machine
An aluminum extrusion machine consists of a machine base, front column, bolster column, extrusion barrel, a hydraulic system controlled by electrical components, and additional components such as die holder, mandrel, scale plate, slide plate, and more.
Classification of Aluminum Extrusion Methods
Aluminum extrusion methods can be classified based on various factors such as the type of metal in the extrusion barrel, stress-strain conditions, extrusion direction, lubrication status, extrusion temperature, extrusion speed, type or structure of the die, shape or number of billets, and shape or number of the final products. These classifications include forward extrusion, backward extrusion (including plane deformation extrusion, axis-symmetric deformation extrusion, and general three-dimensional deformation extrusion), lateral extrusion, glass lubrication extrusion, static hydraulic extrusion, continuous extrusion, and more.
Forward Hot Deformation Extrusion
The majority of hot deformation aluminum material production companies use forward hot deformation extrusion methods with specific dies (flat dies, conical dies, split dies) to obtain aluminum materials that match the desired cross-sectional shape. This is the only method employed by Jin Haochun Aluminum Industry for aluminum material production so far.
The forward extrusion process is simple, equipment requirements are not high, it offers high metal deformation capacity, a wide range of production, strong control over aluminum material properties, high production flexibility, and easy maintenance and correction of dies. However, it has drawbacks, such as strong friction between the extrusion barrel’s inner surface and the aluminum material, leading to higher energy consumption, increased heat generation in the barrel affecting the stability of profiles, reduced production efficiency, limitations on extrusion speeds for aluminum and aluminum alloys, accelerated wear and reduced lifespan of extrusion dies, and uneven structural and performance characteristics in the final products.
Types, Properties, and Uses of Hot Deformation Aluminum Alloys
Hot deformation aluminum alloys can be categorized into eight major classes based on their properties and usage requirements, each with different performance and applications.
Pure Aluminum (Series L) corresponds to the international grade 1000 series pure aluminum. It offers excellent workability, corrosion resistance, surface treatment, and electrical conductivity but has lower strength. It is used for household items, electrical products, pharmaceutical and food packaging, transmission and distribution materials, and more.
Hard Aluminum (Ly) corresponds to the international grade 2000 AL-Cu (aluminum-copper) alloy series. It is used for large components and brackets, with a high copper content and relatively poor corrosion resistance.
Corrosion-Resistant Aluminum (LF) corresponds to the international grade 3000 AL-Mn (aluminum-manganese) alloy series. It cannot be strengthened by heat treatment but offers good workability, corrosion resistance comparable to pure aluminum, improved strength, good welding performance, and is widely used in daily items, construction materials, and devices.
Special Aluminum (LT) corresponds to the international grade 4000 AL-Si (aluminum-silicon) alloy series. It is primarily used for welding materials, characterized by a low melting point (575-630 degrees), good flowability, and fluidity.
Corrosion-Resistant Aluminum (LF) corresponds to the international grade 5000 AL-Mg (aluminum-magnesium) alloy series. It cannot be strengthened by heat treatment, offers corrosion resistance, good weldability, excellent surface gloss, and can achieve different strength levels by controlling the magnesium content. It is used for decorative materials, advanced devices, vehicles, ships, construction materials, and welding components for chemical plants.
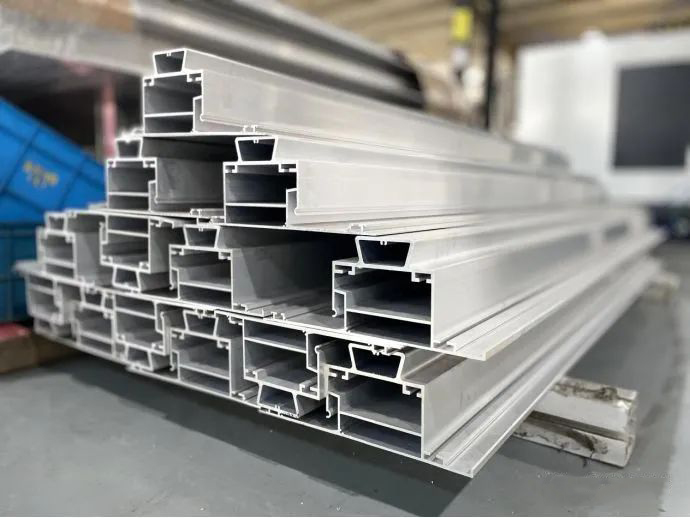
6000 AL-Mg-Si Alloy Series: This alloy can be strengthened by precipitation hardening (Mg2Si precipitation hardening). It offers good corrosion resistance, moderate strength, excellent hot workability, and is mainly used as extrusion material for construction profiles. It exhibits good forming properties and can achieve higher hardness through quenching. It is a major material source in the industry.
Super Hard Aluminum (LC) corresponds to the international grade 7000 AL-Zn-Mg-Cu (aluminum-zinc-magnesium-copper) high-strength aluminum alloy and AL-Zn-Mg welding component alloy. It offers high strength, excellent welding and quenching properties but has lower resistance to stress corrosion cracking, requiring appropriate heat treatment for improvement. The former is mainly used in aircraft and sports equipment, while the latter is mainly used in welding structural materials for railway vehicles.
8000 (AL-LI) Aluminum-Lithium Alloy Series: This series has a lower density (8%-9%) than the 7000 series, providing high rigidity, high strength, and lightweight properties. It is primarily used in military applications such as aircraft, missiles, and engines. This series is still under development, and the aluminum alloy’s resistance to decay under complex conditions has not been completely overcome.
Understanding Solid and Hollow Aluminum Profiles
The processing techniques and extrusion methods for hollow and solid aluminum profiles are fundamentally similar, with the main difference lying in the molds used. For solid aluminum profiles, molds only need to be machined with shaping holes to facilitate extrusion using the extrusion machine. In contrast, for hollow aluminum profiles, the mold consists of two parts: the upper mold and the lower mold. The lower mold is machined to form the outer shape of the aluminum profile, while the upper mold is shaped to create the hollow portion, and there is also a welding chamber designed between the upper and lower molds. To allow aluminum to enter the mold cavity, the upper mold is equipped with diversion holes. Aluminum flows into the welding chamber through these diversion holes, where it re-welds under high temperature and pressure before being extruded through the die holes, resulting in the desired hollow aluminum profile. Since hollow aluminum profile molds consist of two parts, they are often referred to as combination molds or, in some cases, diversion molds due to the presence of diversion holes on the upper mold.
Addressing Low Hardness in Industrial Aluminum Profiles
Controlling hardness during the production and processing of industrial aluminum profiles is crucial. Any deviation from the specified hardness can cause problems for end-users. Here are some methods to address this issue:
Frame Loading: Ensure that the loading of aluminum profiles into the furnace is not too dense. There should be spacing between profiles, especially for small, non-ventilated, and thick profiles. When loading tube profiles along with small or flat profiles, placing the tube profiles at the bottom is advantageous for heat circulation.
Temperature Setting and Control: Set and control the temperature carefully. There may be some deviation between the set temperature and the actual furnace temperature. Adjust the set temperature based on the actual furnace temperature, and closely monitor temperature fluctuations.
Aging Heat Treatment: Conduct aging heat treatment strictly according to the prescribed process. The aging time should be appropriate to prevent under-aging or over-aging, which can result in inadequate hardness.
Separate Aging for Special Alloys: When combining 6000 series aluminum alloys with other special alloys, separate the aging process for each alloy type. If necessary, use the specific process for special alloys when conducting aging.